Impulseの組立不良分析は、AIによる画像認識と分析を活用して、製造品の組立不良を自動的に検出します。製品の各部位を精密に検査し、組み付けミスや部品の異常をリアルタイムで識別し、製造過程の品質向上に貢献します。
Impulseによる組立不良検査
組立時の動画データや、組立製品の静止画データを取得し、良否判定を自動かつ高速に行うことができます。組立作業中の画像解析により迅速な是正対応が可能になります。
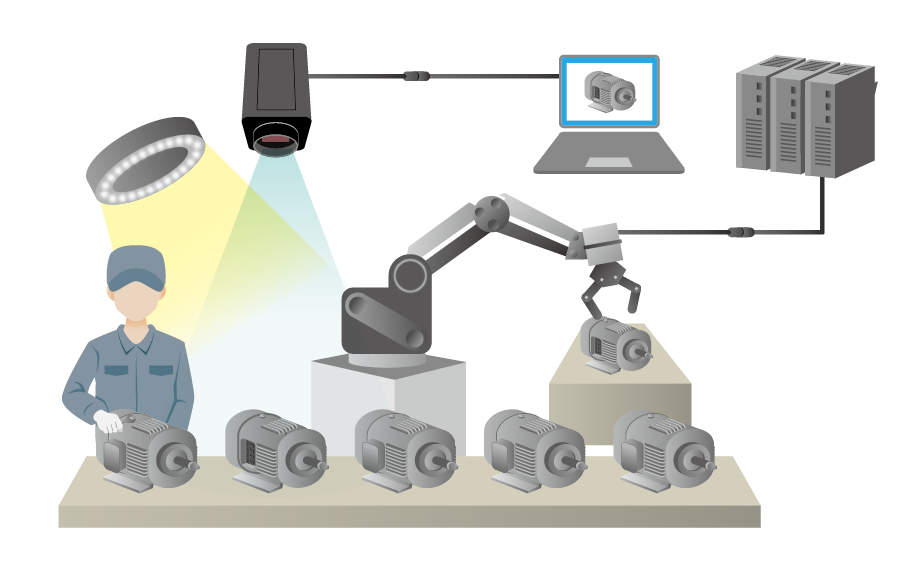
主な検査対象
自動車メーカー(完成系)
-
エアバッグの取付不良
-
配線の接続ミス
-
部品の取付ミス
-
エンジン部品の取付不良
自動車部品業界
-
ネジの締め忘れ
-
配線間違い
-
ガスケットの取付忘れ
-
ギアの誤品
電子機器業界
-
ワイヤーハーネスの接続間違い
-
ケースの歪みネジの締め忘れ
-
センサの配置ズレ
-
基板部品の配置ズレ・誤品
ユースケース
自動車部品:車載電子機器
Impulse による異常検知技術によって、撮影による照明ムラや、製品の組付け誤差を吸収しつつ、数十μm程度の微細な異常を検出。誤検知を1〜2%以内に抑えることに成功。
課題
- 車載電子機器の樹脂やガラス部分に発生するホコリ、キズ、指紋、油染みなどの微細な異常を検出することが困難であった。
- 既存のルールベースの検査方法や他のAIソリューションでは、過検出(誤検知)が頻繁に発生し、精度の向上が求められていた。
取り組み内容
- 最新の異常検知アルゴリズムを用いて、照明のムラや組付け誤差などの見た目のばらつきを吸収し、より精度の高い外観検査を実現。
- 画像を細分化し、総合判定を行うことで、非常に微細な異常箇所の検出を可能にした。
導入効果
- 検査の誤検知率を1〜2%以内に抑え、大幅な精度向上を達成。
- 新規品種に対するモデルの作成や、既存モデルの調整を現場ユーザーが自ら行えるようになり、柔軟な対応と迅速な検査体制の構築が可能になった。
製造業:機械要素部品の組立工程
Impulse による高度な部品認識技術によって、作業工程内でのリアルタイムな組付けミスの防止を実現。少ない学習量によって少量多品種にも対応可能。
課題
- 機械要素部品の組立工程において、各部品の向き・配置・有り無しに対して、目視検査での不良流出が課題となっており、検査の標準化及び自動化が求められていた。
- 熟練度の違いによる点検品質の安定性が不足していた。
取り組み内容
- Impulseを利用して物体検知(特に向き、位置、有無の判定)を可能にし、未知の品番に対しても柔軟に対応できるようにした。
- 組付判定を効率化するため、作業台で静止すると自動撮影し推論処理を行うシステムを開発し、結果をタブレットで確認できるようにした。
導入効果
- 組付け間違いの流出を防ぎ、検査工程前の組立工程の品質改善を実現し、作業者の心理的負荷を軽減。
- 現場の運用性が向上し、人に依存しない運用が実現。さらに、トレーサビリティの観点からも、データ蓄積による組付ミス防止が可能になった。
電子機器:プリント基板の表面実装におけるマウント/はんだ付け工程
Impulseによる高精度な部品認識技術によって、プリント基板のパーツ配置やはんだの不良を検出。簡単な登録・設定でインラインでの少量多品種検査にも対応可能。
課題
- 目視検査による検査時間の短縮を図りたい。
- 検査の難易度が高く、0.1mm単位のズレや、繊細な文字・テクスチャの違いの見逃しが発生していた。
- 少量多品種のため、従来の検査装置では費用対効果が合わず、外観検査装置の導入にもハードルがあった。
取り組み内容
- Impulseを導入し、コンベア上を流れる基板を常時監視し、部品の認識と部品間の位置関係や向きを判定。
- 1品種に対して2,3分の登録で自動検査の設定が完了し、検査時間の大幅な短縮につながった。
導入効果
- 目視検査をImpulseの自動検査に置き換えることで、検査コストの低減、後工程に対する不良の発生を抑制できた。
基本機能
検査方法
- インライン検査、オフライン検査どちらにも対応
- 動画検査により、効率的な全数検査を実現
分析可能なデータ
組立時の動画データや、組立製品の静止画データを元に良否判定を実施します。
-
動画データ
-
静止画データ
解析結果(アウトプット)
画像解析により製品の良否判定と異常箇所の検知を行います。
-
良否判定
-
異常箇所
現場担当者でも簡単に扱えるAIソフトウェア
基本機能に加え、どなたでも使いやすいようにサポート機能が豊富にあります。
-
検査範囲の設定が可能
-
生画像のデータ保存
基本的なシステム構成
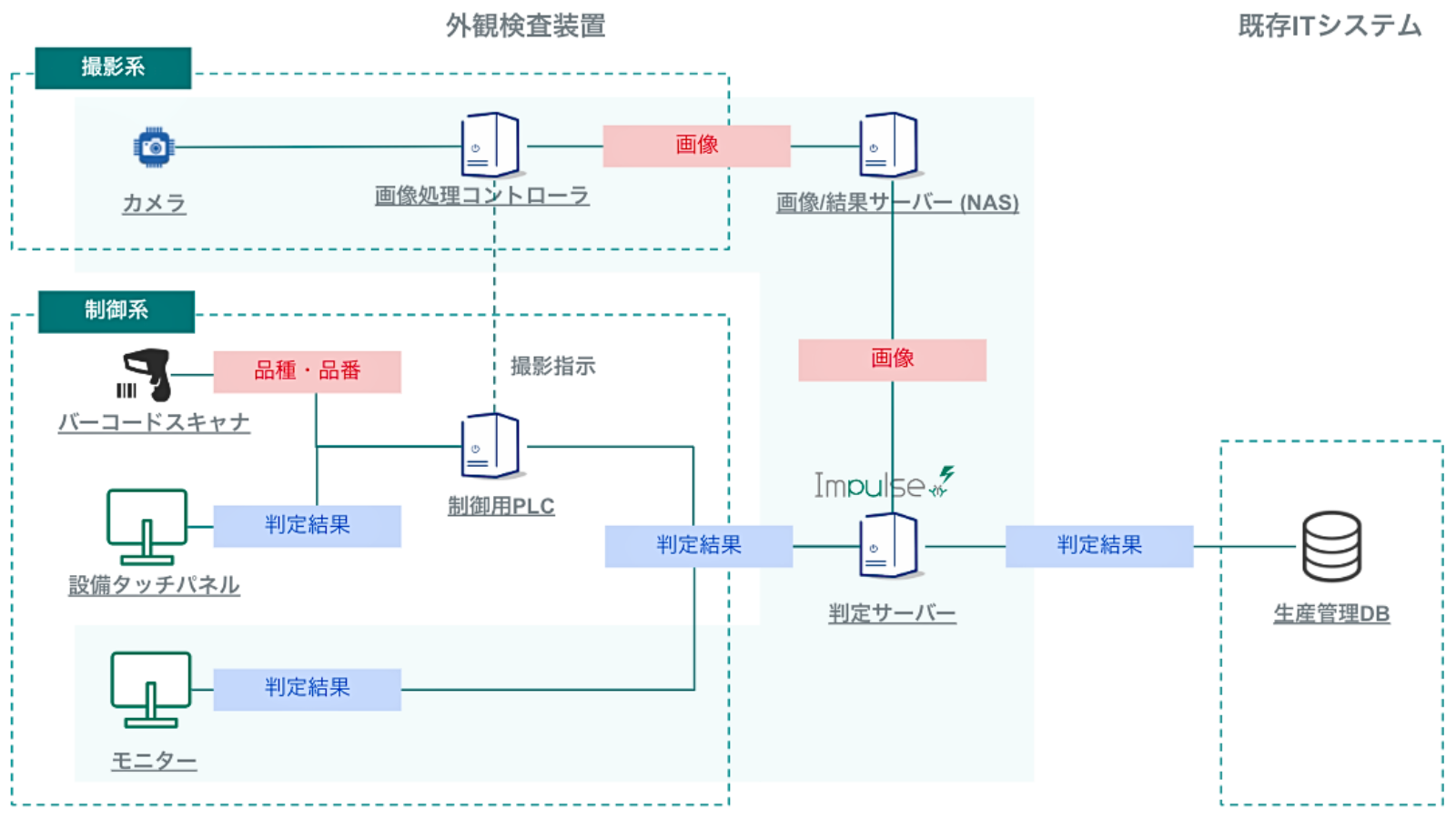
※カメラやPLCをはじめ、様々なメーカーの機材に対応しています。
よくある質問
-
-
A. 検査対象の大きさや検査項目にもよりますが、200〜500万画素のカラーカメラを用いるケースが多いです。弊社からの貸し出しや、現地での撮影検証による選定も支援しております。多くのIPカメラやUSBカメラに対応しておりますので、既にお持ちのカメラを活用したい場合はご相談ください。
-
-
-
A. 検査対象を上から俯瞰する位置に吊り下げる形で設置する場合が多いです。キズ検査や意匠検査なども行う場合は、さらに近接した位置に設置する場合もあります。
-
-
-
A. 扱えます。動画データの中から判定に必要なシーン・フレームを抽出します。またフレームレートは 5〜10程度で十分な場合が多いです。
-
-
-
A. 検証段階では20〜30枚程度から分析を始め、必要に応じて100枚以上学習させる場合もあります。
-
-
-
A. 組付不良検知においては、部品の取り違い、組付け向き、位置、キャップの閉め忘れ等の状態や、取り付け忘れ等を検知することができます。
-
-
-
A. 少量多品種のお客様での導入実績もございます。導入当初はいくつかの品種・品番に限定して判定を行い、データの蓄積に伴って対応範囲を拡大するような進め方が多いです。またモデルも、部品ごとや、ある程度似通った品種ごとに共通化できる可能性もございます。
-
導入の流れ
PoCを実施した後、トライアル運用を経て本稼働に入ります。
※横にスクロールしてご確認ください
-
step1課題の明確化
お問い合わせ -
step2プレ分析 or
実現性検証(PoC) -
step3精度向上と
トライアル運用 -
step4本番稼働
既設ラインと新設ラインの導入フローは以下の通りです。
- 既設ライン
-
- データ受領
- 簡易分析トライアル・連携方法検討
- N増し検証
- 開発
- 新規ライン
-
- ワーク受領
- 撮影機材選定、治具・搬送方法検討
- N増し検証
- 開発