Impulseの外観検査は、AIを活用して製造や生産現場の目視検査を自動化し、微細な不良品をスピーディーかつ正確に検出するシステムです。この技術により、品質保証の精度が向上し、検査に要する時間とコストが削減されます。
Impulseによる外観検査
製品の動画データやの静止画データを取得し、良否判定を自動かつ高速に行うことができます。教師なし学習で高い精度を持って良否判定ができるため、不良データの膨大なインプットが不要です。
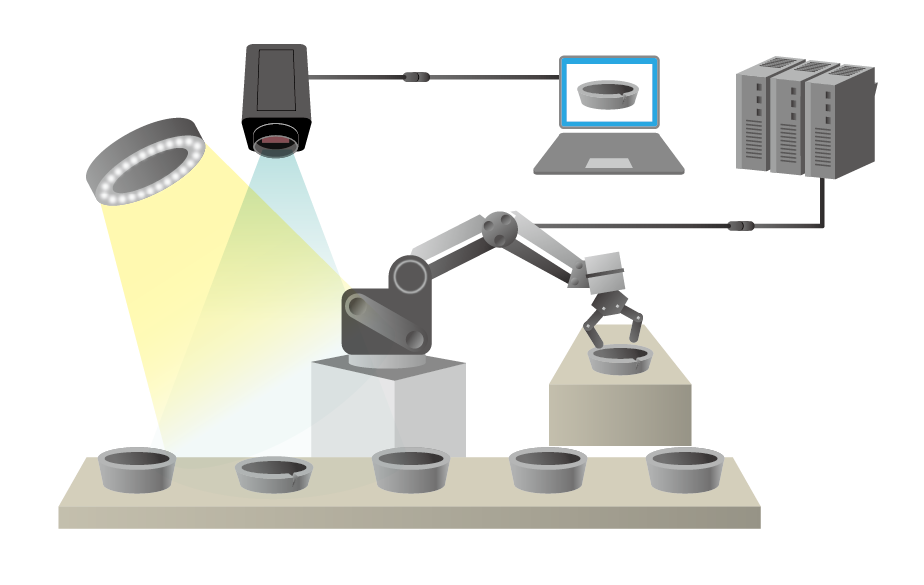
主な検査対象
※横にスクロールしてご確認ください
外観検査項目 | 内容 | |
---|---|---|
分類1 仕様・形状・構造に関わる問題 |
形状 | 指定形状との差異・変形・欠損など |
構造 | 組立や組み合わせの差異・位置ずれなど | |
寸法 | 指定寸法との差異など | |
色 | 色目・色調の差異、変色や色ムラなど | |
意匠・印刷 | 指定の意匠・印刷との差異 | |
分類2 表面形状に関わる問題 |
表面の見栄え・感触 | 凹凸・シワ・筋・艶・ムラ・クモリ・劣化・異触感など |
傷 | 表面に発生した傷や擦れなど | |
付着物 | 汚れやチリ、異物などの付着 | |
分類3 仕上がりに関わる問題 |
仕上がりの丁寧さ | バリや突起、欠け、加工跡など |
自動車メーカー(完成系)
-
ボディの傷・へこみ
-
塗装のムラ
-
ボンネットの浮き
-
メーターの表示不良
自動車部品業界
-
ネジの締め忘れ
-
溶接不良
-
寸法の不一致
-
形状の欠損
電子機器業界
-
機器表面の傷
-
成形品の湾曲
-
液晶の欠陥
-
部材のバリ
ユースケース
自動車部品メーカー:樹脂製精密部品の最終検査工程
Impulseの高精度な異常検知技術により、樹脂特有のテクスチャと傷・打痕を自動的に識別。検査の自動化を実現し、品質の標準化と省人化を達成。
課題
- 樹脂特有の色ムラや表面形状のばらつきが、傷や打痕との区別を困難にしている。このため、目視検査の品質にばらつきが生じている
- 大量生産下での微細な検査が要求されるため、作業者の負担が非常に高くなっている。
取り組み内容
- 新規の検査工程の検討にあたって、色ムラや反射などの正常のばらつきが小さくなるような撮影条件を設計。
- 見た目の特徴が異なる領域に分割し、領域ごとの異常検知モデルを作成。また微細な傷を検出するために、各領域を細分化。
導入効果
- 検査品質の標準化と目視検査の省人化を実現。
- さらなる精度向上のため、蓄積された画像データを用いて定期的な再学習を実施。
- 異常箇所を明確に表示することで、二重チェックの効率化も可能に。
自動車部品メーカー:セラミック製品の自動検査における傾向監視・再学習支援
Impulseのモデル運用プラットフォームを活用して、画像データの特徴変化を分析し、再学習プロセスの効率化を実現。
課題
- 既存の教師あり学習AI製品を用いたものの、データの一元管理や性能指標の明確化、学習モデル作成の工数低減など、AI製品のメンテナンス工数が膨大になる問題が存在した。
- 過検出の大量発生や目視検査コストの増加、本質的な要因の解明が困難であることなどが課題として挙げられる。
取り組み内容
- Impulseの機能群を用いて、各種データの一元管理、性能指標の明確化、学習モデル作成の工数低減を目指したモデル運用プラットフォームを開発。
- 検査装置で撮影された画像に対し、輝度やAIが抽出した特徴量を可視化・傾向分析し、精度向上に寄与する学習データを自動的に抽出。
導入効果
- 設備での判定状況の可視化と製品不良への到達時間の短縮、再学習の効率化に成功。
- 特徴量の可視化により、過検出の原因調査において、検査装置の問題か製品特性の変化かを定量的に分析できるようになった。
建材・住宅設備メーカー:住宅用建材の最終検査
Impulseの高度な異常検知技術によって、建材の表面検査を自動化し、不良の流出を防止。
課題
- 住宅用建材の最終検査工程において、手作業による傷や汚れの検査は時間がかかり、一貫性が欠ける。
取り組み内容
- Impulseの画像処理技術とAIを組み合わせて、フローリング材の表面の欠陥をリアルタイムで検出。
導入効果
- 検査プロセスの自動化により、生産効率が向上し、人的ミスが削減された。
- 品質管理の精度が向上し、顧客への信頼性が高まる。
建材・住宅設備メーカー:疑似異常データの生成による学習支援
既存の教師あり学習システムにインプットするNG画像を、過去のNG画像から生成することで、NGサンプルの収集コストを低減。
課題
- 外観検査において教師あり学習を用いるものの、実際の異常データの収集が難しく、その結果、検査装置の検知精度が望むレベルに達していない状況があった。
取り組み内容
- 既存の検査装置をそのまま利用しつつ、「Impulse」の疑似異常データ生成機能を導入して不足していた異常データを補い、検査精度を向上させる。
- 明るさや位置ずれなど、検査結果の傾向を把握できるデータ管理プラットフォームを構築し、より洗練された検査プロセスを確立。
導入効果
- 疑似異常データの活用により、検査装置の異常検知精度が顕著に向上し、多品種にわたる効率的な検査を可能にした。
- 検査結果の傾向分析を通じて、現場の運用性が大幅に改善され、検査プロセスが人の経験や判断に依存しない形での運用が実現した。
基本機能
検査方法
- インライン検査、オフライン検査どちらにも対応
- 高い検査精度(数十マイクロほどの微細なキズの判定実績あり)
- 静止画だけでなく、連続撮影によってコンベア上などの動くモノに対する検査も可能。
分析可能なデータ
製品の動画データや静止画データを元に良否判定を実施します。
-
動画データ
-
静止画データ
解析結果(アウトプット)
画像解析により製品の良否判定と異常箇所の検知を行います。
-
良否判定
-
異常箇所
現場担当者でも簡単に扱えるAIソフトウェア
基本機能に加え、どなたでも使いやすいようにサポート機能が豊富にあります。
-
検査範囲の設定が可能
-
生画像のデータ保存
基本的なシステム構成
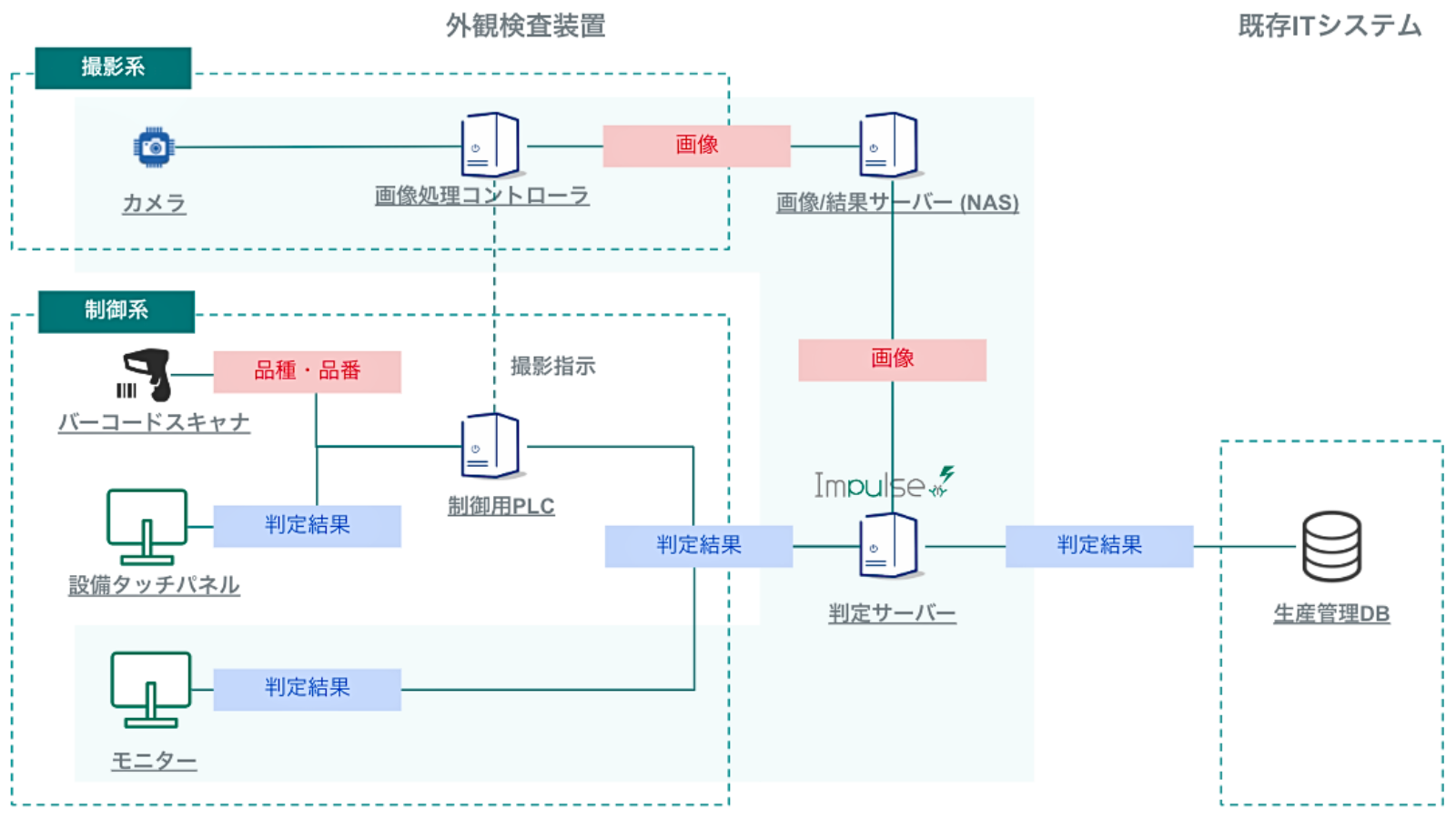
※カメラやPLCをはじめ、様々なメーカーの機材に対応しています。
よくある質問
-
-
A.分析対象の具体的なテーマ(解決したい課題)と関連するデータのご準備をお願い致します。データがない場合でもご相談頂けます。
-
-
-
A.いわゆる良品学習を主に採用しており、学習は OK データのみから可能ですが、検知精度を評価するためには 1 枚以上の NG データが必要です。
-
-
-
A.目安としては OK 20 枚程度, NG 1 枚から検証可能です。PoC では問題設定応じて、100 毎単位の N 増しによる精度改善・検証を行う場合が多いです。
-
-
-
A.検査対象の大きさにもよりますが、弊社に送付いただいて簡易的な撮像を実施することは可能です。
-
-
-
A.実現性検証(PoC)においては、撮像機材があれば実施可能です。オンプレでの設備導入を行う場合は、Impulse が稼働するサーバーが必要になります。
-
-
-
A.実現性検証(PoC)におよそ2ヶ月、導入までに3ヶ月程度が一般的です。ただし設備導入を行う場合は、昨今の半導体不足の影響により納期が遅延する傾向にあります。
-
-
-
A.弊社のご提供範囲は基本的にはソフトウェアになりますが、パートナー企業様と一緒に検査装置としてご提案可能です。治具は自社で作成可能・まずはテスト機として開発したいなど、状況に合わせてご提案差し上げます。
-
-
-
A.お客様の要件に基づき、導入構成をご提案いたします。Impulseはオンプレミス・クラウド、どちらでも構築することが可能です。
-
-
-
A.お客様自身でのモデル生成なども行っていただけます。導入フェーズにおいて一連のモデル運用に関する技術説明をいたします。
-
-
-
A.導入後の保守やサポートももちろん行っております。具体的な内容については別途お伝えさせて頂きます。
-
-
-
A.可能です。設備開発の際にお客様の要件に合わせてカスタマイズにて対応しております。
-
-
-
A.画像の分解能と正常のばらつき度合いにもよりますが、3~5ピクセルで表現されるホコリの検出実績がございます。
-
-
-
A.アルゴリズムや学習データにも依りますが 0.1 msec 〜 1.5 msec 内で推論を行う場合が多いです。また検査要件 (精度・タクトタイム) に応じてベストなアルゴリズムを選択可能です。
-
-
-
A.動画データを用いた外観検査や設備監視の実績がございます。
-
-
-
A.OK/NG の判定結果と合わせて、モデルが NG と判断した異常箇所を表示することが可能です。
-
導入の流れ
PoCを実施した後、トライアル運用を経て本稼働に入ります。
※横にスクロールしてご確認ください
-
step1課題の明確化
お問い合わせ -
step2プレ分析 or
実現性検証(PoC) -
step3精度向上と
トライアル運用 -
step4本番稼働
既設ラインと新設ラインの導入フローは以下の通りです。
- 既設ライン
-
- データ受領
- 簡易分析トライアル・連携方法検討
- N増し検証
- 開発
- 新規ライン
-
- ワーク受領
- 撮影機材選定、治具・搬送方法検討
- N増し検証
- 開発